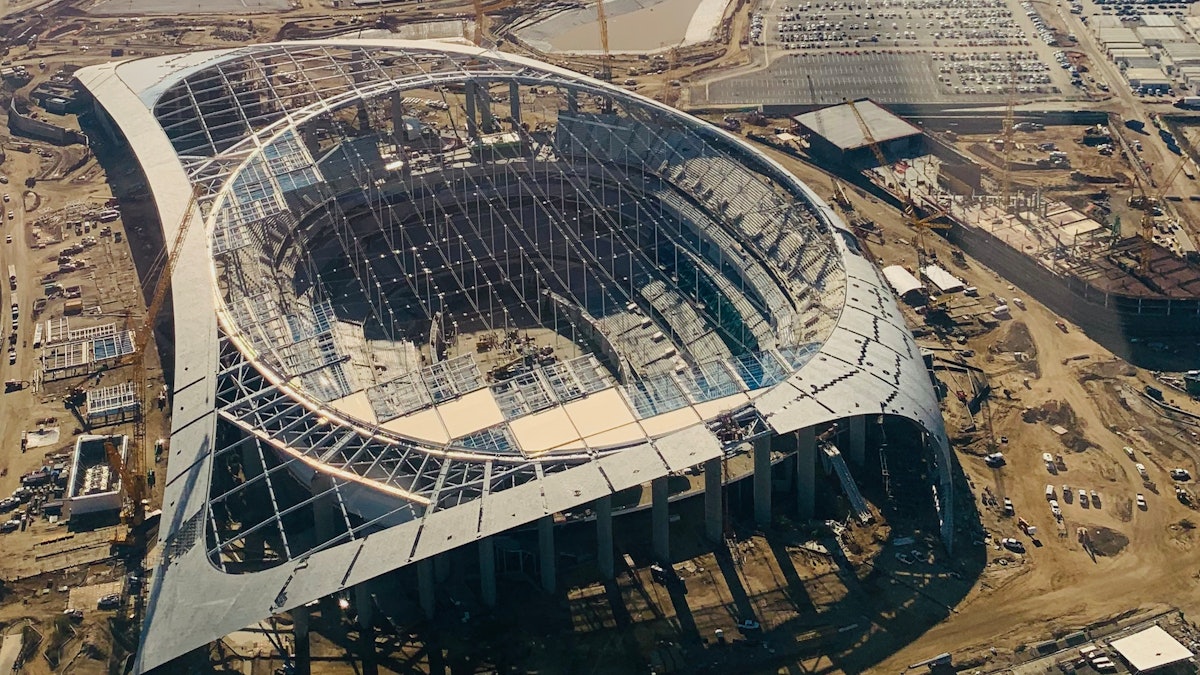
In the wake of the global COVID-19 pandemic, construction materials such as steel—a necessary material for use in traditional concrete applications—have been significantly impacted by price increases and material shortages. While this may be concerning for businesses and municipalities that are set to begin, or are in the process of, construction projects involving parking decks, roads, bridges, and other concrete-related repairs, it may actually be a benefit in disguise as they can now utilize the short-term and long-term benefits of fiber-reinforced concrete.
The Euclid Chemical Company
Fiber-reinforced concrete is a concrete mixture that is reinforced with randomly oriented fibers. Depending on the project and the environmental impact that may affect the concrete, there are a wide variety of fibers that will specifically fit the needs of your specific project. Some of the available fiber types are as follows.Available fiber products for concrete reinforcement from Euclid Chemical are “grouped” PSI Fiberstrand Fibers, TUF-STRAND Macro-Synthetic Fibers, and PSI Steel and Blended Fibers.The Euclid Chemical Company
Synthetic Macrofibers: Used in applications to replace conventional reinforcing for flooring, precast and shotcrete applications. Steel Fibers: Generally used to provide concrete with enhanced toughness and post-crack carrying capacitySteel & Micro/Macro Blends: A combination of steel and/or macro-synthetic fibers with various micro-synthetic fibers that help control plastic shrinkage cracking, while also providing enhanced toughness and post-crack load carry capacityGlass Fibers: Predominantly used in architectural applications and modified cement-based panel structures Cellulose Fibers: Processed wood pulp product that is used for the control and mitigation of plastic shrinkage cracking
Over the past several years, we have seen an increased interest in the use of fiber-reinforced concrete in concrete pavement applications, such as parking lots, bridge decks, and roadways. Organizations like the American Concrete Institute, the American Concrete Pavement Association, and the National Concrete Pavement Technology Center have developed guidelines and recommendations on how to properly select and use fiber in concrete. (Guidelines are available for purchase.)
ACI PRC-544.4-18: Guide to Design with Fiber-Reinforced Concrete
NCPTC Fiber-Reinforced Concrete for Pavement Overlays
NCPTC Overview of Fiber-Reinforced Concrete Bridge Decks
While it may seem like a new development in construction, fiber-reinforced concrete has in fact been around for several decades. However, as municipalities and businesses seek a low-cost option that will provide durability and the ability to develop state-of-the-art designs, there has been a rise in the use of fiber-reinforced concrete.
Examples of projects that have used fiber-reinforced concrete include SoFi Stadium, the home stadium of the Los Angels Rams and Los Angeles Chargers, and highway rehabilitation in Fowler, Ind.
The SoFi stadium, located in Inglewood, Calif. was constructed by a joint venture between general contractor Turner Construction and AECOM Hunt. The concrete contractor was Morley Builders, architect HKS Inc., engineer Walter P. Moore, and the ready mix producer was CalPortland.The Euclid Chemical Company
SoFi Stadium is the home to the Los Angles Rams and Los Angeles Chargers football teams. The stadium seats 70,240 spectators for most events, with the ability to expand it with 30,000 additional seats for larger events. It is located at the former site of the Hollywood Park Racetrack in Inglewood, 3 miles (4.8 km) from Los Angeles International Airport. TUF-STRAND SF at a dosage of 5 lb/yd³ (3 kg/m³) was used as the reinforcement in topping slabs for the upper-level decks of this facility. These fiber-reinforced slabs, as opposed to conventionally reinforced slabs, will not have the potential for corrosion over the lifetime of this facility. TUF-STRAND SF synthetic macrofiber was also used to provide improved crack control for this topping slab. Additionally, construction time was reduced as the use of TUF-STRAND SF eliminated the time to crane lift and install welded wire fabric or reinforcing steel, and job-site safety was improved by eliminating a potential tripping hazard for the concrete placement crew.
US52 being rehabilitated with fiber-reinforced concrete.The Euclid Chemical CompanyThe Indiana Department of Transportation (INDOT) is also utilizing fiber reinforcement with thin concrete overlays for highway rehabilitation. Constructed in 2018, the section of US52 outside of Fowler, Indiana, was rehabilitated with a 4 to 4.5-in. concrete overlay using a 4 lb/yd3 (2.4 kg/m3) dosage of Euclid Chemical’s TUF-STRAND SF macro-synthetic fiber. This 4-lane highway was previously surfaced in asphalt and had reached a deteriorated state that required a long-term solution and improved ride quality. Irving Materials, Inc. serviced this project by utilizing a twin-shaft portable mixer placed at their local dry batch plant location. This combination of mixers allowed for the production of up to 100 yd3 per hour with Superior Construction placing between 500 – 900 yd3 per day. In total, over 18,500 yd3 of FRC pavement was placed without the use of any dowels or reinforcing steel showcasing a major market potential for future FRC and pavement projects.
Key Benefits of Using Fiber-Reinforced Concrete
As you plan your next concrete-related construction project, here are the seven key benefits of fiber-reinforced concrete that both you and your clients should consider.
Cost-Effectiveness: According to the National Concrete Pavement Technology Center, “fiber-reinforced concrete can offer a cost-effective, sustainable solution for resurfacing and rehabilitating existing pavements. Either as overlays or full-depth replacement pavements, state DOTs and other engineering groups are rapidly adopting macro-synthetic fibers into their designs, specifications, and experimental projects for road and airfield pavements.”
Less Staff Required: With the limitations on available manpower and cost uncertainties affecting the construction industry following the pandemic, fiber-reinforced concrete can offer a safer and more cost-effective working environment that can actually speed up construction while reducing the environmental impact at a project site. From the perspective of safety, having fewer personnel on site and reduced trip hazards are significant benefits and allow for increased speed of placement.
The Euclid Chemical Company
Reduced Delays: By subtracting the use of conventional steel rebar, an inspection of the steel placement is not required by a municipality. The concrete would be placed with fiber reinforcing supplied by a concrete provider and installed in the concrete prior to placements. Ready-mix trucks can quickly and efficiently place the concrete at the required project location with minimal finishing practices needed.
Improved Long-Term Serviceability: Concrete can be susceptible to corrosion, freezing and thawing, attacks by traditional road salt, and penetration of other aggressive solutions. Concrete durability can be improved by minimizing the ability of water and other solutions from penetrating beyond the surface. Fiber-reinforced concrete helps maintain tight crack control, which helps reduce the size of a crack’s width—ultimately preventing water and other solutions from penetrating the concrete.
Temperature & Shrinkage Reinforcement: Fiber-reinforced concrete can be used as an economically viable alternative to welded wire reinforcement and small diameter bars to guard against temperature and shrinkage issues.
Reduced Cost: Fiber-reinforced concrete can reduce construction times, reduce the cost of labor, and lower maintenance costs—which is not only beneficial for contractors but those savings can then be passed along to customers in the form of reduced cost for the completed project. In addition, contractors can inform that fiber-reinforced concrete significantly reduces the cost of ongoing maintenance.
Environmentally Friendly: Similar to old tires and athletic footwear being recycled to be used in synthetic athletic turf fields, fiber-reinforced concrete can be an environmentally friendly solution. Due to steel fibers being made of steel—which is made from iron, a natural depleting resource—the high cost of steel may not be justified, especially with the reduced maintenance cost associated with fiber-reinforced concrete. Recycled steel fibers may represent a more environmentally friendly, cost-efficient approach.
Research has shown that recycled steel fibers, which are made from products such as recycled car tire rims, can provide similar results as commercially made steel fibers—at a fraction of the cost. Along with minimizing landfill waste, the cost savings provided by using recycled steel can be passed along to customers as well.
As the uncertainties of the COVID-19 pandemic remain, fiber-reinforced concrete not only serves as the future of the construction industry, but as a viable solution to protect the health and safety of construction personnel, and the financial bottom lines of businesses and municipalities.
About the author
Michael Mahoney is a professional engineer and the director of marketing and technology, fiber reinforced concrete for the Euclid Chemical Company in Cleveland, Ohio. He is a fellow and member of the American Concrete Institute and has served on various committees for the National Pre-Cast Concrete Association and American Society for Testing and Materials.